- The plastic industry maintained a stable trend despite pressure in the first half of the year!
- Detailed introduction of polyester Masterbatch of Longkou Huacai Plastic Industry Co., LTD.!
- Longkou Huacai Plastic Industry Co., LTD. Polypropylene Masterbatch: Specialized Coloring Solution for Polypropylene materials!
- Nylon masterbatch: A material that endows nylon products with rich colors!
- Core composition, key performance requirements, application scenarios and usage methods of nylon masterbatch!
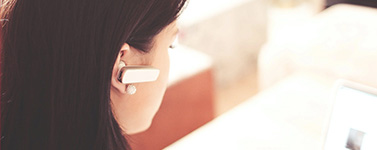
- Tel: 0086-13705451607
- Fax: 0086-0535-8719999
- Email: lkhc668@sohu.com
- Add: East Heping, High-tech Zone, Longkou City, Shandong Province
Longkou Huacai Plastic Industry Co., LTD. Non-woven Fabric Color Masterbatch: The engine of color and Function in the Textile Industry!
In modern textile industry, non-woven fabric color masterbatches, as a key coloring and functional modification material, are increasingly demonstrating their irreplaceable value. This plastic colorant, which is made by dispersing a high proportion of pigments or additives with thermoplastic resins through a special process, not only endows non-woven fabrics with rich color expressions, but also enhances multiple properties such as antibacterial, hydrophilic and flame retardant through functional addition. The core value of non-woven fabric color masterbatch lies in its "pre-spinning coloring" technology route. Compared with the traditional post-dyeing process, this technology has significant environmental advantages such as water and electricity conservation and no wastewater discharge. According to industry estimates, it can reduce the operating costs of chemical fiber producers by 50%.
From the perspective of technical composition, high-quality non-woven fabric color masterbatches rely on three key elements: efficient dispersion of pigments, optimal selection of carrier resins, and scientific proportioning of additives. The particle size of pigments usually needs to be controlled below 1 micron. They are wet ground through special processing equipment and stabilized coated with ultra-high dispersants that are compatible with polypropylene resin to prevent pigment agglomeration caused by surface free energy during the spinning process. Carrier resins are mostly made of materials such as polypropylene or polyethylene. They not only need to have good thermal stability to adapt to the high-temperature spinning environment, but also must maintain excellent compatibility with the substrate to be colored. The additive system may include various functional components such as UV anti-aging agents, lubricants, and antibacterial agents depending on the final application. The precise proportion of these materials and the processing technology jointly determine the final performance of the color masterbatch.
In terms of production technology, the manufacturing of modern non-woven fabric color masterbatches has formed a highly automated assembly line operation mode. A typical production process includes precise weighing of raw materials, high-temperature mixing, extrusion molding, water cooling, drying, pelletizing and screening, etc. Among them, the drying process is particularly crucial. Advanced drying equipment adopts a waste heat recovery system, precisely controlling the hot air flow by adjusting the opening degree of the air guide plate. This not only ensures the drying quality but also avoids energy waste. Extrusion technology is also constantly innovating. Some equipment achieves raw material premix through a conical mixing feed bucket design, combined with a hollow stepped shaft cooling system, significantly enhancing production efficiency and product consistency.
In terms of application performance, high-quality non-woven fabric color masterbatches need to meet multiple strict indicators. The heat resistance temperature usually needs to reach 200-260℃ to withstand the high temperature during the spinning process. The filtration value (DF) should be controlled below 0.2barc·cm²/g to ensure smooth spinning. The lightfastness should reach grade 5 or above, and the migration resistance should be grade 4 or above to ensure that the products do not fade or get contaminated during use. For non-woven fabric color masterbatches used in medical applications, they also need to have excellent biocompatibility and stability to avoid irritating human tissues or causing allergic reactions.
With increasingly strict environmental protection regulations and diversified market demands, non-woven fabric color masterbatch technology is developing in two main directions: one is green and sustainable, including the development of bio-based degradable color masterbatches and the use of recycled raw materials, etc. The second is functional integration, achieving the combination of multiple functions such as antibacterial, temperature-sensitive, and antistatic through means like nanotechnology and microencapsulation. In the future, with the penetration of intelligent manufacturing technology, the production of non-woven fabric color masterbatches will become more precise and efficient, and the degree of color and function customization will also be further enhanced, providing the textile industry with more diverse material solutions.
- Detailed introduction of polyester Masterbatch of Longkou Huacai Plastic Industry Co., LTD
- The plastic industry maintained a stable trend despite pressure in the first half of the y
- Longkou Huacai Plastic Industry Co., LTD. Polypropylene Masterbatch: Specialized Coloring
- Nylon masterbatch: A material that endows nylon products with rich colors!
- Core composition, key performance requirements, application scenarios and usage methods of
- What is nylon masterbatch?
- Longkou Huacai Plastic Industry's polypropylene color masterbatch at the Beginning of Autu
- Polypropylene masterbatch: Longkou Huacai Plastic Industry Co., LTD. 's ideal choice for p
- Longkou Huacai Plastic Industry Co., LTD. Polyester Masterbatch: A stable coloring choice
- Analysis of the Current Situation and Development Prospects of China's Plastic Products In